
Forest

River

Tradition
From Raw Materials Cultivation to World-class Tosa Washi Creation
Making washi (Japanese paper) with qualities perfect for preservation while continuing the pursuit of the essence of Tosa washi
Kashiki Paper Co., Ltd.
(Kochi Prefecture)
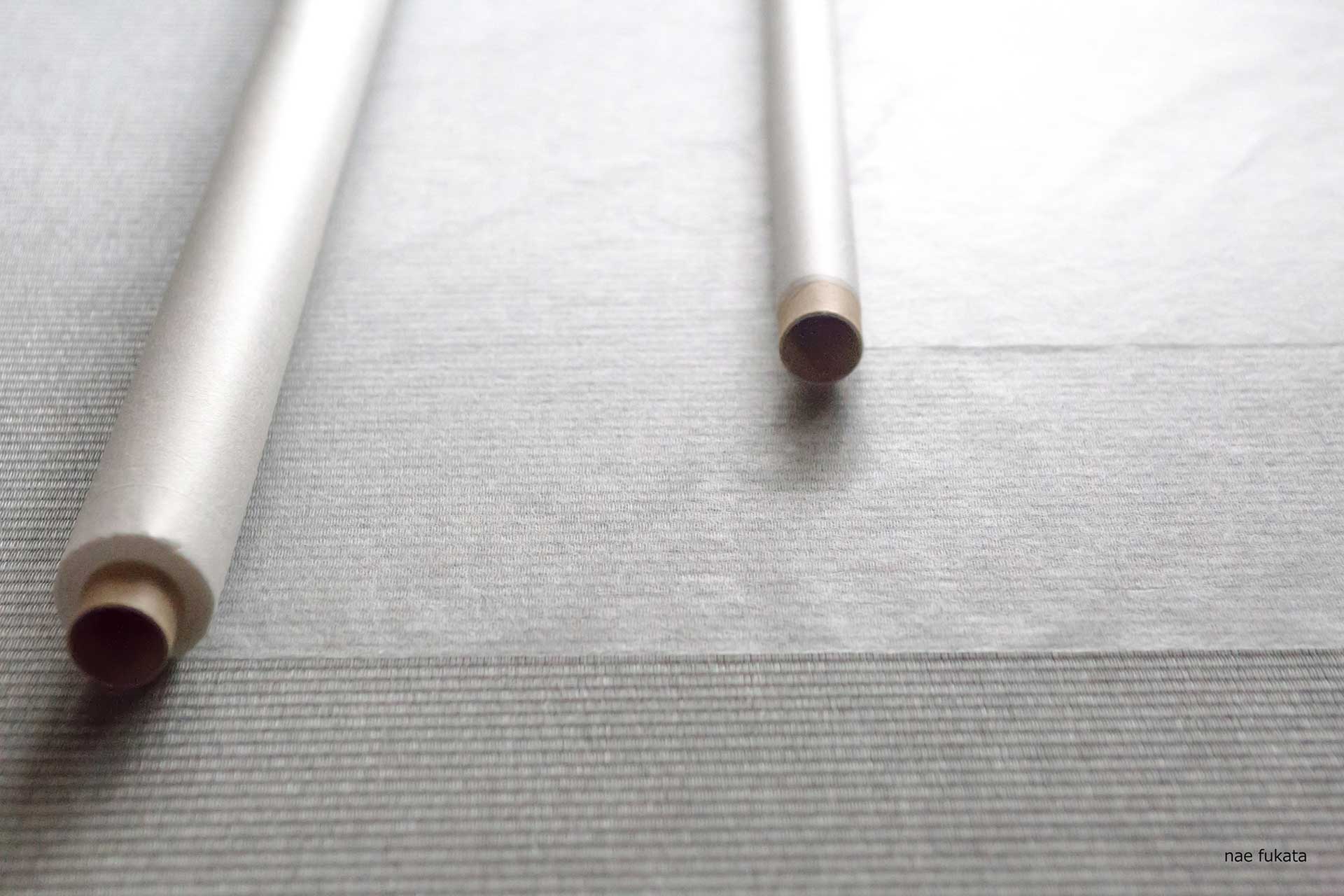
Overview
Since its founding in 1950, Kashiki Paper Co., Ltd. has been producing high-quality Tosa washi in Ino-cho, Kochi Prefecture, Japan by both hand and machine using domestically produced kozo, mitsumata, and gampi (mainly from Kochi Prefecture). For over 1,000 years, Tosa washi has been made in Kochi Prefecture (historically, Tosa Province) in the Shikoku region of Japan using the bast fibers of plants such as kozo and is one of Japan’s three major washi paper styles. The “Special Thin Tosa Washi for Cultural Heritage Repair” washi developed in 1982 by Kashiki Paper is used for repairing cultural heritage sites around the globe.
Recently, Kashiki Paper has also started the cultivation of raw materials. The background behind this initiative is the decline in the production of raw materials within the prefecture, due to a drop in demand for washi paper in general. It has become common for washi manufacturing companies to procure raw materials from outside the prefecture or from overseas; however, washi is originally made using natural resources such as plants, water, wood ash, limestone, etc., from the local area. Furthermore, the techniques and culture passed on in each distinct area are what form the basis of washi manufacturing. Kashiki Paper has continued to pursue the essence of Tosa washi, valuing the techniques and spirit of washi-making as handed down from generation to generation, along with being involved in the entire process from raw materials cultivation to manufacturing.
Successful outcomes
- Demand is growing not only within Japan but also overseas.
- Kashiki Paper's main machine-made washi, "Kashiki Washi (Shinpu)," is used in a wide variety of fields, such as by art conservators and book designers, calligraphy artists, printmakers, designers, and for architecture-related applications.
- Kashiki Paper supports a theater company, Washi+ that organizes plays and dance workshops for elementary and middle school students during summer breaks with the theme of Tosa washi from 2016.
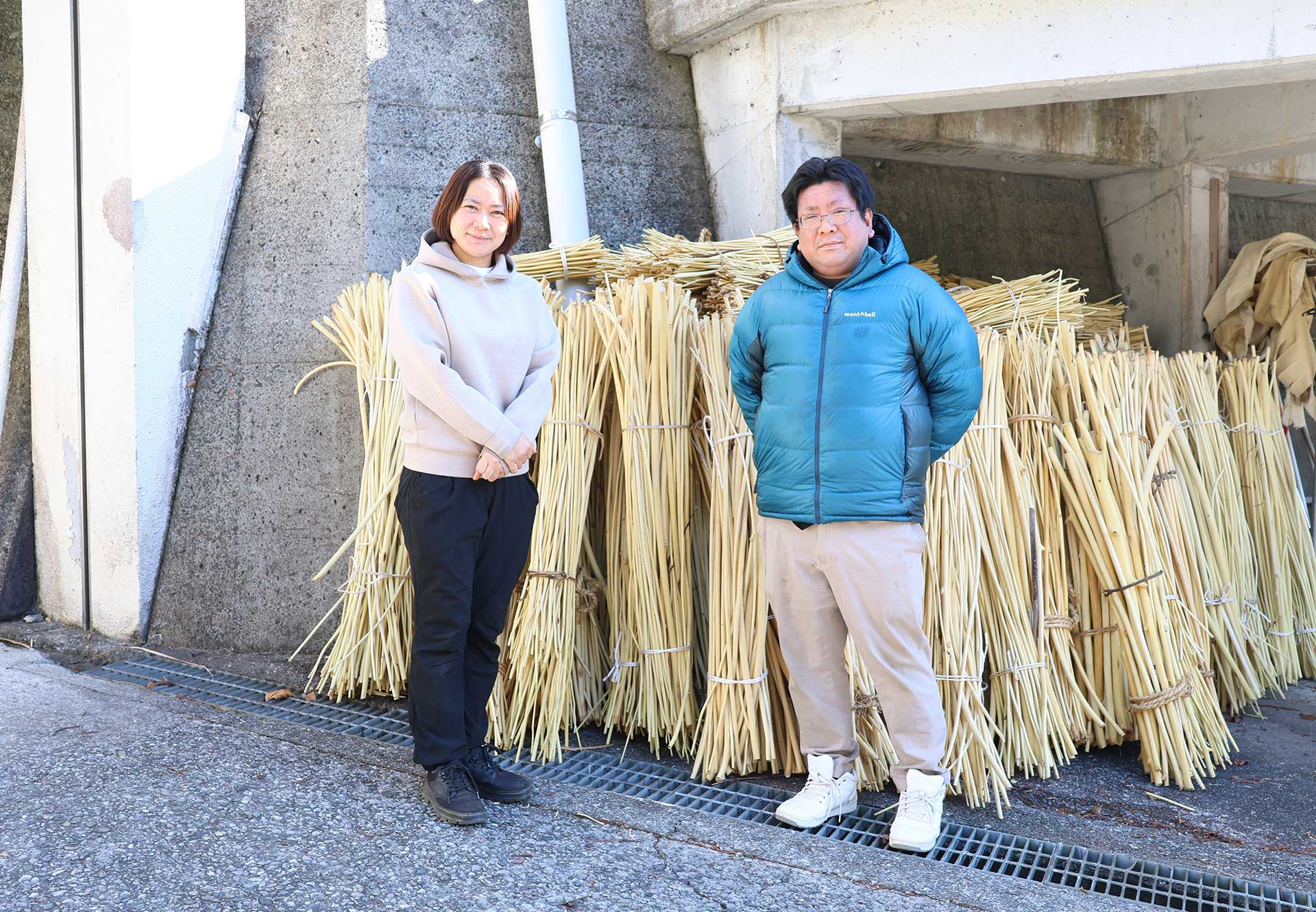
Continuing to make washi that can be trusted and contributing to work that is passed down to future generations
“Good paper is made from good materials.” Kashiki Paper’s representative, Hiromasa HAMADA, together with his sister, Ayumi HAMADA, has followed this belief as passed down from generation to generation, concentrating on procuring raw materials from trusted producers across Japan. Currently, more than 90% of the needed raw materials are procured within Kochi Prefecture, of which the company cultivates around 30% of the raw materials.
Washi demonstrates strong regionality—with washi being named after the areas where the paper is produced, such as Tosa washi, Echizen (Echizen City, Fukui Prefecture) washi, and Mino (Mino City, Gifu Prefecture) washi. Each is now recognized as its own washi brand. Kochi Prefecture is rich in resources such as water and the raw materials necessary for washi-making, and the town of Ino-cho, where Kashiki Paper is located, has prospered through washi manufacturing. There are 17 washi companies in Kochi Prefecture, and many are located in Ino-cho. Tosa washi is used for a wide variety of applications, such as for nihonga (Japanese-style paintings), printmaking, calligraphy, fittings, mountings, wrapping paper, and more.
Kashiki Paper was founded in 1950; however, the Hamada family has made a living by making washi paper since the mid-1800s. The company has been making washi both by hand and by machine. Even when they use a machine, the processing of the raw materials, such as the steaming of the mulberry and the peeling of the skin, is done manually just as when washi is made by hand. Furthermore, to achieve quality equivalent to that of handmade washi, Kashiki Paper has put in effort to make high-quality washi of various thicknesses, from extremely thin to thick (3 g/m2 to 100 g/m2). One of their products, the “Shinpu” mulberry paper, is sold for approx. 1,900 yen per 1 m2.
Hiromasa says: “It had been said that paper made via Western methods lasts 100 years and that washi lasts 1,000 years. Qualities of preservation are the essence of washi. I want to pay particular attention to the raw materials and continue to make washi that can be trusted and that will contribute to works that are passed on to future generations.”
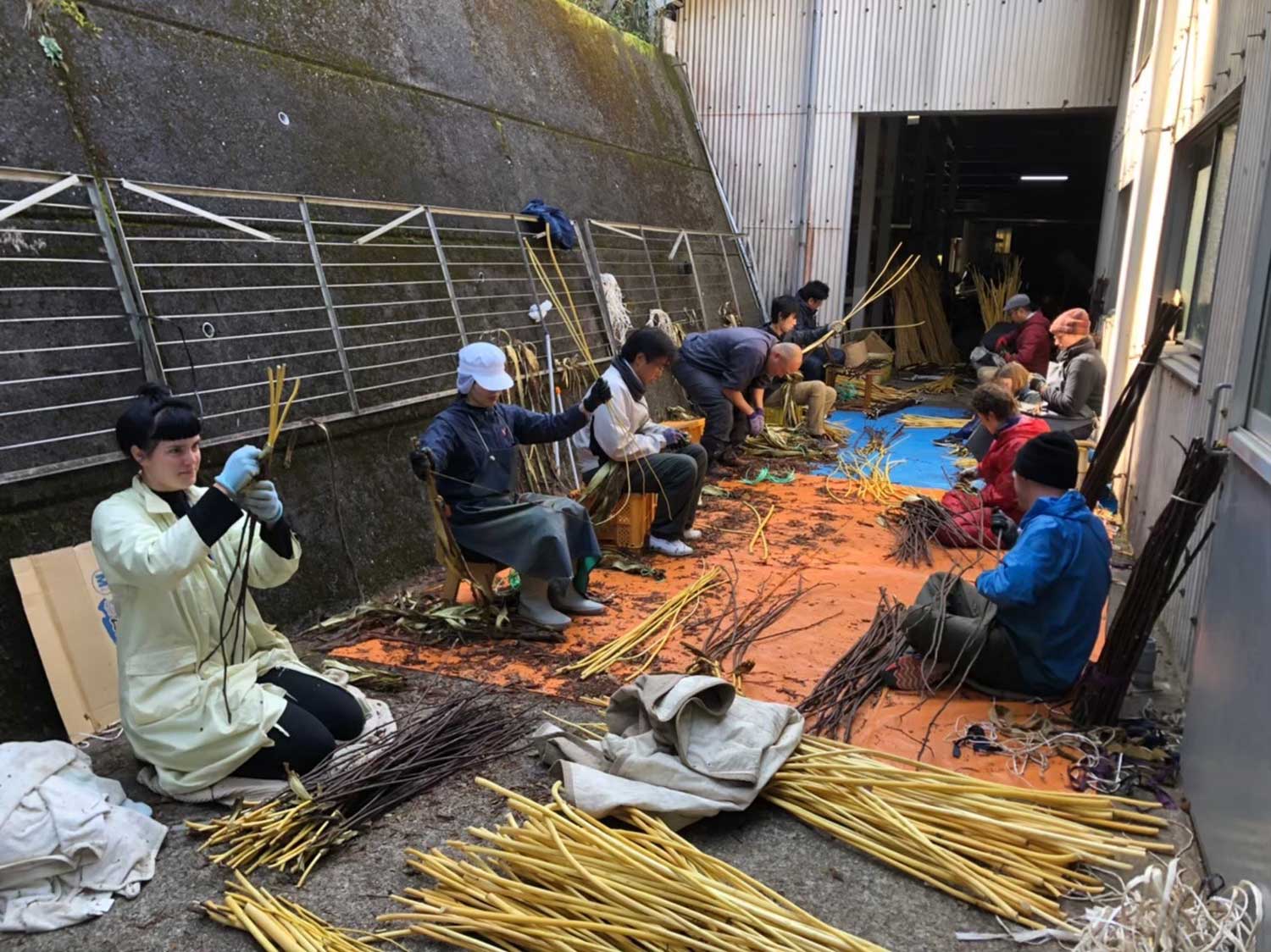
The year of 2017 was a turning point for the company. One raw materials producer decided to stop production due to the old age of its craftsmen, making it difficult for Kashiki Paper to procure the necessary raw materials for the year. From there, with the guidance of the producer, Kashiki Paper began working with employees and volunteers (neighbors, artists from within and outside the prefecture, resident volunteers, etc.) to perform the processes of cultivation, harvesting, and steaming and stripping, which had heretofore been done by other producers. Overcoming the challenges, Kashiki Paper is on the way to mastering Tosa washi-making.
Kashiki Paper has set its mission as: “Aiming to work together with the local community to enliven and pass on the culture brought about by Tosa washi raw materials and the clear waters of the Niyodo River.” Ayumi, who is also an actor, runs a research-based artist-in-residence program that provides artists from around the world with an environment where they can learn how the people involved in Tosa washi have lived and experience harvesting raw materials and making washi. In addition, she has invited artists and dancers from around the world, organizing performances with the theme of Tosa washi and mulberry, etc. Ayumi says: “I want to use dance and performing arts to shed light on the parts and people behind the scenes who are involved in making washi, along with the voices that have not yet been heard.”
During the interview, both repeatedly emphasized: “Everything is thanks to the people around us.” Being grateful to those who support us, to carry out work that can be trusted, to understand the times, and respond to the changes… it is these attitudes that have kept the company going to date.
Tosa washi creation
Kashiki Paper Co., Ltd.
https://kashikiseishi.com/index.html